Александр Навроцкий - Ковка
- Название:Ковка
- Автор:
- Жанр:
- Издательство:Array Литагент «АСТ»
- Год:2014
- Город:М.
- ISBN:978-5-17-081801-3
- Рейтинг:
- Избранное:Добавить в избранное
-
Отзывы:
-
Ваша оценка:
Александр Навроцкий - Ковка краткое содержание
Книга предназначена для студентов, обучающихся по специальности «Технология художественной обработки материалов», и тех, кто желает порадовать себя и своих близких красивыми изделиями из металла, изготовленными самостоятельно.
Ковка - читать онлайн бесплатно ознакомительный отрывок
Интервал:
Закладка:
Существует несколько типов топоров: плотничный массой 0,5–1,8 кг, столярный с прямым лезвием массой до 0,5 кг; лесорубный массой 1,2–1,8 кг, колун массой до 2 кг, а также пожарный, универсальный, хозяйственный, любительский и т. п.
Топор (рис. 1.2.7 а ) состоит из металлического бойка – головки (п. 1 ) и деревянного топорища (п. 2 ). Головка, в свою очередь, имеет обух (п. 9 ), лезвие (п. 5 ), бородку (п. 3 ), конический разрез для выдергивания гвоздей (п. 4 ). Топорище (рукоять) состоит из захватной, головной и хвостовой частей. Для соединения головки с топорищем имеется проушина (п. 7 ), куда вставляется обработанная на пологий конус головная часть топорища и расклинивается металлическим «заершенным» клином (п. 6 ).
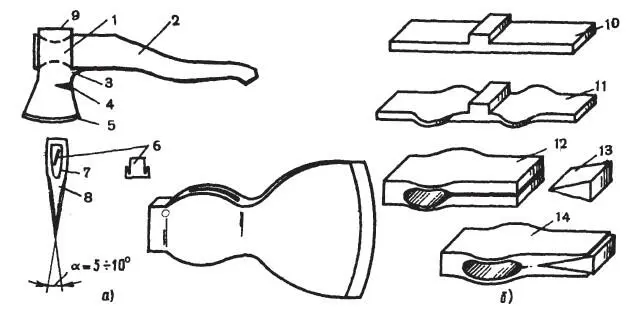
Рис. 1.2.7. Топор (а), технология ковки головки топора (б).
Для цельнокованого топора берут квадратный металлический брусок сечением 50× 50 мм из сталей 45, 50 или У7. Нагревают заготовку до ковочной температуры и при помощи прошивня и оправок пробивают отверстие. Затем вставляют специальную оправку и оформляют проушину, затем отделывают щеки и обух. После чего обрабатывают лезвие, надрубают и отгибают бородку.
Последовательность ковки сварного топора показана на рис. 1.2.7 б , п. 10–14 . Берем полосу толщиной 10–12 мм и шириной 40–50 мм и, оставив в средине заготовки участок 40 мм (п. 10 ), протягиваем края заготовки до толщины 5–6 мм, затем разгоняем щечки (п. 11 ) и сгибаем топор, как показано на рисунке (п. 12 ). После этого отковываем клин из инструментальной стали У7-У8 и ввариваем его в основу топора (п. 14 ).
Рекомендации по кузнечной сварке см. в Приложении В. Если кузнечная сварка прошла успешно, то можно окончательно проковывать всю головку топора.
Тесак. Технология его изготовления значительно проще, чем топора. Берем полосовую сталь толщиной 5–6 мм, надрубаем полоску (рис. 1.2.8 а ), отгибаем и оттягиваем ее «на острие» (рис. 1.2.8 б ) под черенок для ручки. Рабочую часть резака оттягиваем к лезвию, после чего пробиваем отверстие, оформляем обушную часть (рис. 1.2.8 в ) и насаживаем ручку.
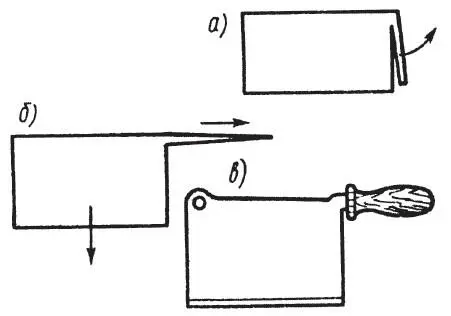
Рис. 1.2.8. Изготовление тесака.
Железные косыизвестны в России с IX–XI вв., и ковались они в сельских кузницах из кричного железа. Заводское производство кос началось на Урале только в 1809 г. на Артинском заводе, а уже к 1880-м гг. косы и серпы делали в Вятской, Пермской, Владимирской, Тверской, Ярославской и других губерниях.
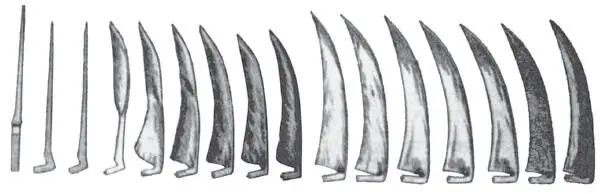
Рис. 1.2.9. Технология изготовления косы.
На рис. 1.2.9 представлены основные технологические стадии изготовления косы. Вначале из полосы оттягивают конец (процесс ковки идет с верхнего ряда слева направо), затем отгибают ушко и выдавливают зубец. После этого начинают оттягивать лезвие путем расковки полосы. Процесс расковки ведут в четыре этапа: нагрев и расковка носовой части; второй нагрев, поворот косы и ковка с другой стороны; третий нагрев и общая расковка и, наконец, окончательная расковка и загибка обуха. После этого начинают отделку острия в два нагрева.
Дальнейшую отделку ведут в холодном состоянии. Косу правят и выравнивают молотом. После обрезки лезвия «начисто» косу калят в масле и отжигают. Затем косу отбивают (наклепывают) молотом, полируют и вторично отбивают.
Кованые железные гвоздина Руси применялись уже в X–XI вв., и в это время появилась специальность «гвоздочника», т. е. кузнеца, который кует в основном гвозди. Широкое производство гвоздей, скоб и других изделий для строительства и судостроения начинается в период Петровских реформ в начале XVIII в. В это время куется большой ассортимент гвоздей: корабельные (длиной 250–500 мм), полукорабельные (150–200 мм), брусковые (200–250 мм), тесовые (30–180 мм), кровельные (до 75 мм), обойные (10–12 мм), шпалерные (6–7 мм), а также подковные, штукатурные и др.
Пробовали делать гвозди путем нарезки из листового металла, однако они получались недостаточно качественными. Наибольший скачок в гвоздильном деле произошел в то время, когда для изготовления гвоздей начали использовать проволоку. Первые автоматы для изготовления гвоздей из проволоки появились в Европе в начале XIX в.
В России кузницы, в которых ковали гвозди, называли гвоздарными, а иногда и «мирщинными», так как для производства гвоздей использовали различные листовые обрезки и железный лом, которые собирали «с миру». Собранный металл сваривали кузнечной сваркой, а затем проковывали в полосу и из нее уже делали гвозди.
Технология изготовления гвоздей и болтовво всех кузницах примерно одинакова. Гвозди получают следующим способом: мерные заготовки из проволоки укладывают в щелевую печь для нагрева. После нагрева заготовку (рис. 1.2.10 б , п. 4 ) вставляют в гвоздильню (рис. 1.2.10 б , п. 2 ), установленную на наковальне (рис. 1.2.10 б , п. 1 ) так, чтобы ее верхний высаживаемый конец выходил на требуемую длину а нижний упирался в подставку (рис. 1.2.10 б , п. 5 ). Ударом ручника (рис. 1.2.10 б , п. 3 ) головку осаживают и придают ей заданную граненую форму при помощи шляпного молотка (рис. 1.2.10 б , п. 6 ). Необходимо иметь в виду, что за один удар можно высадить и не согнуть заготовку длиной l, в 2–2,5 раза большей, чем ее диаметр d .
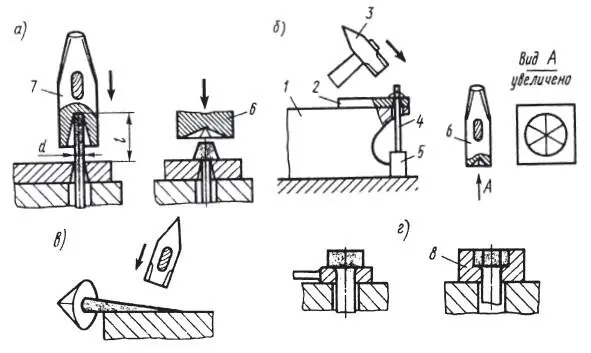
Рис. 1.2.10. Изготовление гвоздей и головок болтов.
Если необходимо изготовить гвозди с большой шляпкой, то вначале для получения небольшого конуса используют специальный подкладной инструмент (рис. 1.2.10 а, п. 7 ) с конусным углублением. А при втором ударе, используя шляпный молоток (рис. 1.2.10 а, п. 6 ), получаем граненую головку. После этого оттягиваем стержень гвоздя (рис. 1.2.10 в ).
Головку болта высаживают аналогично головке гвоздя, но для получения граней ее деформируют в специальной гвоздильне (рис. 1.2.10 г, п. 8 ) с шестигранным углублением.
Гвоздь с большой шляпкой можно ковать, не используя высадку, а путем оттяжки стержня из заготовки с большим сечением, с последующим отрубанием гвоздя от основной заготовки и оформлением головки.
Кузнец из Соликамска А. Малышев предложил еще один способ набора металла для формирования увеличенной головки гвоздя или болта. Для этого необходимо изготовить две специальные оправки (рис. 1.2.11, п. 2, 5 ) с центральным отверстием, диаметр которого совпадал бы с диаметром заготовки. Первая оправка (рис. 1.2.11, п. 2 ) сверху имеет внутренний конус, а вторая (рис. 1.2.11, п. 5 ) – без конуса.
Читать дальшеИнтервал:
Закладка: