Александр Полулях - Грохочение угля
- Название:Грохочение угля
- Автор:
- Жанр:
- Издательство:неизвестно
- Год:2020
- ISBN:нет данных
- Рейтинг:
- Избранное:Добавить в избранное
-
Отзывы:
-
Ваша оценка:
Александр Полулях - Грохочение угля краткое содержание
Грохочение угля - читать онлайн бесплатно ознакомительный отрывок
Интервал:
Закладка:

Для «трудного» зерна размером, приближающимся к размеру отверстия d≈l , получено

где d – размер зерна, м.
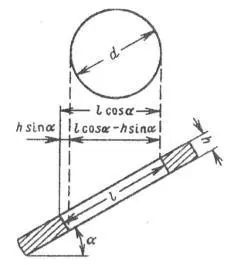
Рис. 1.6. Схема влияния наклона и толщины решета на размер зерна, проходящего в отверстие сита
По формуле (1.10) можно вычислить максимальную скорость сферического тела d≈l , при которой обеспечивается беспрепятственное прохождение его через отверстие.
Предельная скорость движения материала (скорость подачи) по формуле (1.10) получена без учета подбрасывания.
При режиме с подбрасыванием скорость движения зерен повышается в 2–3 раза. Оптимальную подачу устанавливают экспериментально в зависимости от производительности и необходимой эффективности грохочения.
Существенное влияние оказывают на процесс грохочения угол наклона и толщина просеивающей поверхности (рис. 1.6). Если грохочение осуществляется на наклонной под углом α плоскости толщиной h , мм, то для определения размера зерна, проходящего через отверстия, получено выражение

Чтобы получить подрешетный продукт одинаковой крупности при α = 20° и, α = 25° размер отверстий наклонного сита должен быть в 1,15 и 1,25 раза больше отверстий горизонтального сита.
В начальный период грохочения эффективность его увеличивается быстро, а затем замедляется. Это объясняется тем, что скорость грохочения зависит от количества зерен, которые должны пройти сквозь отверстия сита. В первые моменты проходят в основном легкогрохотимые зерна, и процесс грохочения протекает быстро. Затем с течением времени количество их становится все меньше и меньше.
Трудногрохотимые же зерна требуют для своего просеивания значительно больше времени. Поэтому и эффективность просеивания с течением времени замедляется.
С увеличением производительности грохота Q , при прочих равных условиях, эффективность грохочения Е понижается.
Таким образом, на эффективность грохочения влияют, в основном, два фактора: гранулометрический состав грохотимого материала и отверстия просеивающей поверхности грохота. На вероятность прохождения частицы через отверстие оказывают влияние технологические, конструктивные, динамические и гидродинамические факторы.
1.3. Гранулометрический состав
1.3.1. Крупность частиц
При дроблении, измельчении и грохочении приходится иметь дело с рыхлыми смесями частиц материалов (породы) различного размера – от максимальных кусков, измеряемых сотнями миллиметров, до мельчайших частиц величиной в несколько микронов.
Куски обычно имеют неправильную форму и их величина может быть охарактеризована лишь несколькими размерами. Для практических целей желательно характеризовать величину отдельного куска одним размером. Этот размер обычно называют «диаметр» куска. Диаметром кусков сферической формы будет диаметр шара. Для кусков кубической формы за диаметр принимают длину ребра куба; для кусков неправильной формы диаметр определяют по главным измерениям – длине l , ширине b и толщине t параллелепипеда, в который вписывается змеряемый кусок. При этом используют все размеры или только некоторые из них. За диаметр d куска принимают:
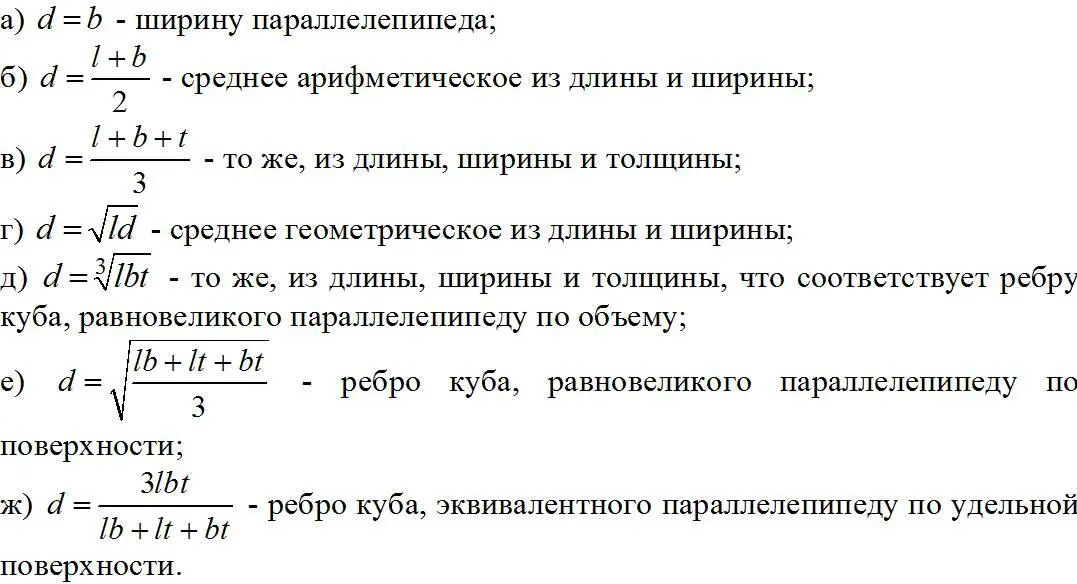
Перечисленные способы определения диаметра куска неправильной формы используются при изучении отдельных кусков. Формула для вычисления выбирается в зависимости от способа измерений и целей, для которых подсчитывается диаметр куска. С помощью сит можно получить один размер куска. В этом случае приходится пользоваться формулой (а). С помощью микроскопа определяется два размера и можно пользоваться формулами (б) и (г). Для крупных кусков можно получить все три размера и применить формулы (в), (д), (е) и (ж), если надо характеризовать линейный размер, объем, поверхность или удельную поверхность соответственно.
При грохочении, для массовых определений размера зерен, за диаметр зерна принимают размер наименьшего квадратного отверстия, через которое это зерно может проходить.
Крупность всей массы сыпучего материала оценивают по содержанию в ней классов определенной крупности, т. е. по ее гранулометрическому составу. Гранулометрический состав материала определяют посредством анализов:
1) ситового – путем рассева на ситах на классы крупности, для материалов крупнее 0,04 мм;
2) седиментационного – путем разделения материала на фракции по скоростям падения частиц в жидкой среде, для материалов крупностью от 50 до 5 мк;
3) микроскопического – путем измерения частиц под микроскопом и классификации их на группы в узких границах определенных размеров для материалов крупностью менее 50 до десятых долей микрона.
Гранулометрический состав материалов для контроля процессов грохочения, дробления и измельчения на обогатительных фабриках определяют чаще всего посредством ситового анализа.
Средний диаметр частиц определенного класса крупности находится по формуле

Для нескольких классов или всей смеси частиц средний диаметр определяется как среднединамический диаметр по формуле

Выход отдельных классов определяется в процентах. Размер крупных и мелких частиц выражается в миллиметрах, а тонких – в микронах.
Номинальным называют размер квадратной ячейки контрольного сита, через которое проходит 95 % пробы материала. Для оценки номинального диаметра помимо прямых измерений используется поведение частицы в некоторых специфических условиях, например осаждение в воде. Некоторые из наиболее известных номинальных диаметров [3] приведены в табл. 1.3.
Очевидно, что полученный диаметр для частицы неправильной формы будет зависеть от используемой методики измерения. Например, диаметр Стокса d Ст определяется при ламинарных условиях потока и не применим при турбулентных потоках, так как в последнем случае частица ориентируется так, чтобы обеспечить максимальное торможение, в то время как в первом случае она ориентируется случайным образом. Поэтому всякий раз при упоминании крупности частиц следует указывать, какой номинальный диаметр используется.
Читать дальшеИнтервал:
Закладка: