Эдвардс Деминг - Выход из кризиса. Новая парадигма управления людьми, системами и процессами
- Название:Выход из кризиса. Новая парадигма управления людьми, системами и процессами
- Автор:
- Жанр:
- Издательство:Array Литагент «Альпина»
- Год:2014
- Город:Москва
- ISBN:978-5-9614-3893-2
- Рейтинг:
- Избранное:Добавить в избранное
-
Отзывы:
-
Ваша оценка:
Эдвардс Деминг - Выход из кризиса. Новая парадигма управления людьми, системами и процессами краткое содержание
Выход из кризиса. Новая парадигма управления людьми, системами и процессами - читать онлайн бесплатно ознакомительный отрывок
Интервал:
Закладка:
Очевидно, что это условие 1. Значит, для минимальной полной стоимости не нужно никакого контроля. Следование рекомендациям Военного стандарта 105D удваивает минимальную полную стоимость. Это легко увидеть по результатам упражнения 5.
Было бы еще хуже, если бы степень статистической управляемости была высока, контроль выборок дал бы не больше информации о партиях, нежели подбрасывание монеты (упражнение 1).
Дополнительные проблемы с измерениями и материалами
Возможная экономия при создании вспомогательных подсистем. В предшествующей теории стоимость k 2 обычно возрастает (возможно 10-кратное увеличение) с каждым этапом работы процесса и может достигать очень высоких значений при окончательной сборке. Иногда можно избежать излишне высоких затрат, создавая подсистемы, которые движутся вдоль потока собранными и формируют финишную продукцию. Некоторые подсистемы, пройдя через контроль и потребовав незначительных замен и регулировки, образуют новую точку отсчета. Стоимость k 2 теперь будет стоимостью контроля и наладки подсистемы. Теория совместно с полезными записями, отражающими опыт, может показать, что некоторые подсистемы вообще не нуждаются в проверке, в то время как другие надо подвергнуть 100 %-ному контролю во избежание роста затрат по ходу процесса. Теория, изложенная в этой главе, позволяет принять верное решение.
Наша цель в предшествующих разделах – показать, что существуют способы минимизации затрат и максимизации прибыли, если руководствоваться правильной теорией.
В то же время мы прилагаем все усилия с целью полного исключения дефектных изделий из процесса. Мы делаем это систематически, сравнивая результаты наших испытаний с результатами поставщика и применяя подходящие статистические методы, такие как x – и R -карты.
Плодотворное сотрудничество с поставщиком деталей, особенно критических, и успешные испытания и регулировка подсистем сводят все основные проблемы при окончательном контроле систем к редчайшим событиям.
Трудности обнаружения редких дефектов. Редкие дефекты трудно обнаружить. По мере того как доля дефектных изделий уменьшается, все труднее определить, насколько мало их число. С помощью контроля нереально обнаружить все дефекты, особенно когда они редки, и это верно как для визуального, так и для автоматического контроля. Нет никаких оснований верить больше изготовителю, который заявляет, что имеет только 1 дефект на 10 000, чем тому, кто декларирует 1 дефект на 5000 изделий. В обоих случаях такую пропорцию трудно оценить.
Так, если бы p было равно 1/5000 и если бы процесс находился в статистически управляемом состоянии, то следовало бы проверить 80 000 деталей, чтобы найти 16 дефектных. Эти данные дали бы оценку = 1/5000 для производственного процесса со стандартной ошибкой √16 = 4, или 25 %. Такая оценка доли дефектных неточна, несмотря на трудность контроля партии объемом 80 000 деталей. Возникает вопрос: оставался ли процесс стабильным в течение всего времени изготовления 80 000 деталей? Если нет, то каков смысл числа 16 дефектных изделий? Трудный вопрос.
Существуют примеры, когда на миллионы деталей нет ни одного отказа либо их число очень мало или они отсутствуют на 10 млрд. Никакой контроль готовой продукции не поможет получить требуемую информацию, когда доля дефектных изделий столь мала. Единственный возможный способ узнать, что происходит при столь крайних требованиях, – это использование контрольных карт с реальными измерениями деталей в ходе процесса. Сто наблюдений, таких как 4 изделия подряд 25 раз в день, дали бы 25 выборочных точек для x – и R -карт. Карты показали бы, идет ли процесс без изменений, или где-то произошел сбой и выпуск ряда изделий надо остановить, пока причина не будет обнаружена. Как только причина найдена, можно принять решение забраковать всю совокупность продукции за определенный период или пропустить некоторые изделия. Все возрастающие возможности x – и R -карт становятся все более очевидными.
Использование резервирования. Иногда возможно и разумно при конструировании сложной аппаратуры поставить две или более детали параллельно, так чтобы, если одна из них откажет, другая автоматически взяла бы на себя ее функции. Две параллельные детали, каждая со средней долей дефектности pi , эквивалентны одной со средней долей дефектности, равной pi 2. Если, например, pi было бы равно 1/1000, то pi 2 равнялось бы 1 000 000. Ограничения на вес и размеры, конечно, могут не позволить использовать резервирование. Существуют и другие проблемы: сработает ли резервная деталь, когда понадобится? Возможно, наилучшее решение – это высокая надежность единичной детали.
Математическая теория отказов и резервирования – чрезвычайно интересный и важный раздел статистики, но мы вынуждены на этом расстаться с данной темой, обозначив лишь ее важность.
Будет ли более недорогой метод контроля действительно дешевле?Вечный вопрос: как уменьшить затраты на контроль, если контроль неизбежен (как при условии 2)? Предположим, что существует основной метод контроля и метод, который обходится дешевле на одно изделие (меньше k 1 ), чем основной. Действительно ли менее дорогой метод дешевле с точки зрения полных затрат? В случае неразрушающих испытаний следует подвергнуть 200 изделий обоим методам и по результатам исследования составить таблицу 2 × 2, как это проиллюстрировано на рис. 48. Каждая точка – это результат двух испытаний одной детали. Точка на диагонали показывает согласие обоих методов. Точки вне диагонали представляют расхождение. Деталь, которая была бы отвергнута основным методом испытаний, но выдержала испытание более дешевым методом (пропуск дефекта), привела бы к отказу системы со стоимостью k 2 . В то же время деталь, которая прошла бы испытание основным методом и была бы отвергнута более дешевым (ложный сигнал), привела бы к затратам, равным u , где u – стоимость одной детали.
Результаты таблицы 2 × 2 легко описать численно. Примем для чисел в четырех ячейках следующую схему расположения:
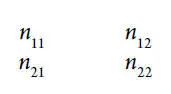
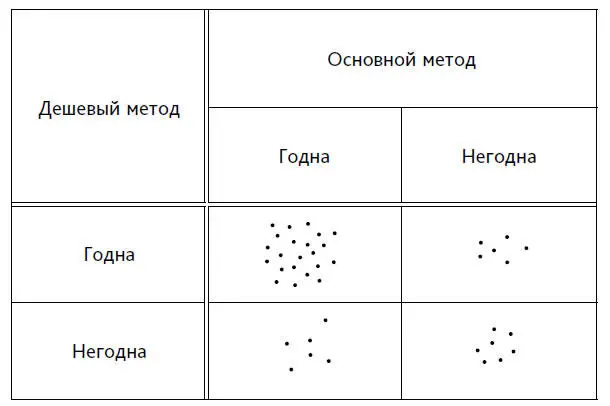
Рис. 48. Таблица 2 × 2 для затрат на испытания ряда изделий двумя методами. Каждые два испытания производят точку в одной из четырех ячеек
Читать дальшеИнтервал:
Закладка: