Эдвардс Деминг - Выход из кризиса. Новая парадигма управления людьми, системами и процессами
- Название:Выход из кризиса. Новая парадигма управления людьми, системами и процессами
- Автор:
- Жанр:
- Издательство:Array Литагент «Альпина»
- Год:2014
- Город:Москва
- ISBN:978-5-9614-3893-2
- Рейтинг:
- Избранное:Добавить в избранное
-
Отзывы:
-
Ваша оценка:
Эдвардс Деминг - Выход из кризиса. Новая парадигма управления людьми, системами и процессами краткое содержание
Выход из кризиса. Новая парадигма управления людьми, системами и процессами - читать онлайн бесплатно ознакомительный отрывок
Интервал:
Закладка:
Особое внимание при 100 %-ном контроле (или просмотре) следует уделить исключению общих причин или взаимодействию между исходной работой и контролем. Руководство должно довести до сведения всех заинтересованных, что нельзя работать с документом, представляющим особую проблему, или с цифрами, которые неясны. Например, не должно быть никакой возможности прочесть 8 как 5. Если цифра не вполне ясна кому-то из сотрудников (это вопрос индивидуального суждения), он должен отложить документ в сторону и оставить его на рассмотрение руководителя. Руководителю для решения данного вопроса, возможно, понадобится поднять соответствующие первичные документы, или сделать письменный запрос, или послать телеграмму, или позвонить.
Если взаимодействие между исходной работой и ее контролем полностью исключено и если исходная работа и ее анализ имеют в среднем одну ошибку на 1000 документов, то вместе эти два процесса дадут среднее значение намного лучше, чем 1/10002 или 1/1 000 000.
Пример ошибочного контроля. Ошибочный контроль приводит к трем типам проблем: 1) разочарование производственных рабочих; 2) неправильная интерпретация точек на контрольной карте; 3) дефектная продукция попадает к потребителю.
Приведенный ниже пример иллюстрирует типичные предпосылки для ошибочного контроля, а также разочарование производственных рабочих. На 17 операторов приходится 4 инспектора. Работа операторов распределяется по инспекторам с помощью случайных чисел.
В таблице 2 показаны результаты контроля, полученные в течение трех недель, а на рис. 22 результаты контроля представлены в графическом виде. Очевидно, что где-то закралась ошибка: характер различия между результатами контролеров вызывает беспокойство. Контролеры 1 и 4 имеют близкие результаты. Согласие наблюдается и у контролеров 2 и 3, однако различие между парами контролеров существенно.
Действенная мера в этом случае – операциональное определение того, что приемлемо, а что нет. Мы сталкивались с этой проблемой в главе 1. Операциональное определение включает в себя метод проверки, пример и критерии, при помощи которых принимается решение о том, может ли проделанная часть работы быть классифицирована как дефектная или как приемлемая (см. главу 9). Операциональное определение – это определение, смысл которого можно передать другим; это язык, с помощью которого люди могут понять друг друга.
Я признателен Дэвиду Чамберсу за оказанную честь работать с ним над этим примером.
Таблица 2
Данные о числе дефектных изделий, обнаруженных в процессе контроля за три недели, по операторам и по контролерам
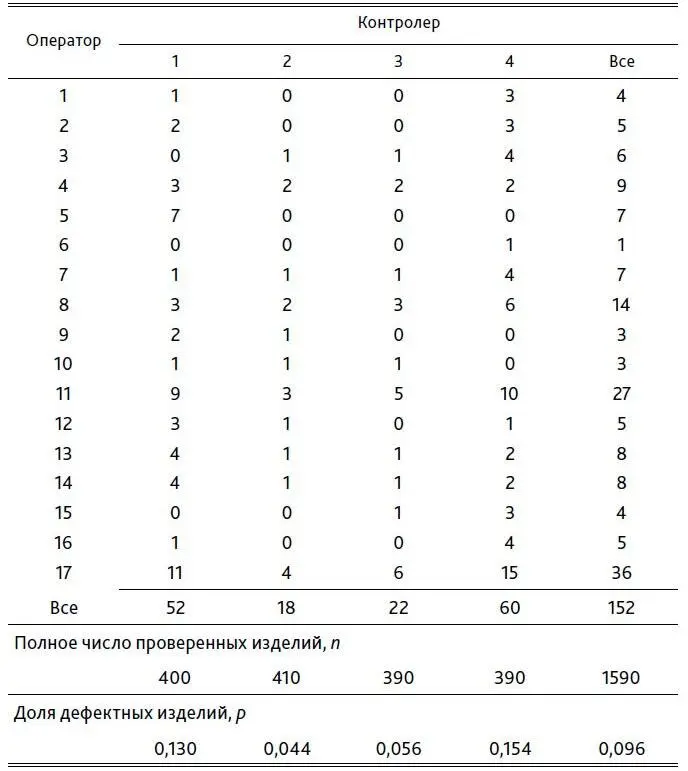
Примечание: коробки с готовыми изделиями (по 5 шт. в каждой) распределялись по контролерам с помощью случайных чисел. Число изделий, произведенных каждым оператором, примерно одинаково.
Ошибочный контроль, вызванный страхом. Контрольная карта на рис. 23 показывает результаты ежедневного контроля в течение двух месяцев для доли дефектных изделий, обнаруженных при окончательной проверке продукции, подготовленной к отправке. Средняя доля дефектных изделий за два месяца составила 8,8 %. Контрольные пределы равны:
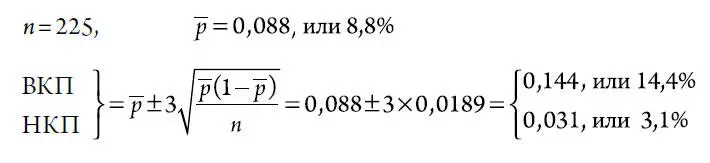
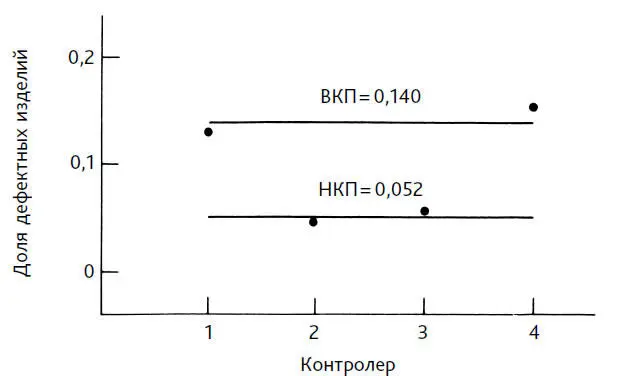
Рис. 22. Представленные на карте в графической форме суммарные результаты для каждого из четырех контролеров свидетельствуют о наличии проблем, связанных с контролем. Вычисление контрольных пределов:
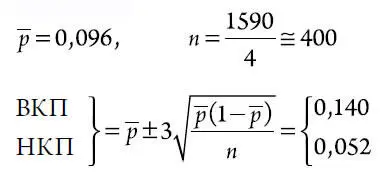
.
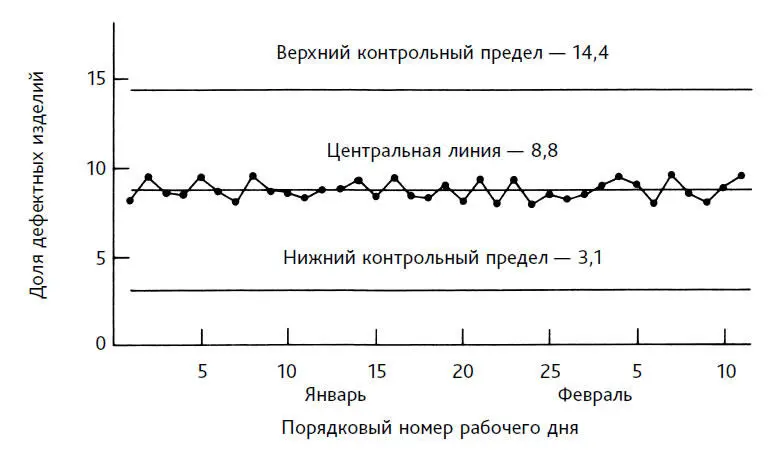
Рис. 23. Ежедневные данные по доле дефектных изделий. В день проверяется 225 изделий
Рисунок 23 демонстрирует любопытную ситуацию. Смещение точек вверх и вниз слишком малó относительно центральной линии. Два возможных объяснения этому:
1. Процесс спроектирован так, что доля дефектных изделий практически постоянна. В общем-то это не редкость. Например, 12 палет штампуют детали по кругу. Одна из них выходит из строя. Остальные 11 продолжают работать. Продукция на выходе будет иметь одну дефектную на каждые 12 штамповок; 1/12 равна 8,3 %, что свидетельствует о нахождении в опасной близости от среднего 8,8 % на карте.
2. Приведенные на карте данные ничего не значат.
Первую версию мы (Дэвид Чамберс и я) отвергли, поскольку детально знаем процесс и сопутствующие ему условия. Второе объяснение кажется нам более правдоподобным. Контролер не чувствовал себя в безопасности, он боялся. По заводу прошел слух, что управляющий закроет завод и уволит всех, как только доля дефектных изделий при окончательной приемке достигнет 10 %. Контролер пытался сохранить работу для 300 человек.
Где бы ни появился страх, мы получим ложные цифры. Организация живет в соответствии с теми представлениями, которые формируются в головах ее сотрудников. Действительно ли этот менеджер высказывал такую угрозу и собирался исполнить ее? На самом деле это не имеет никакого значения. Мы проинформировали высший менеджмент о найденном нами объяснении – страхе. Проблема исчезла, когда управляющий заводом перешел на другую работу, а его сменил новый менеджер.
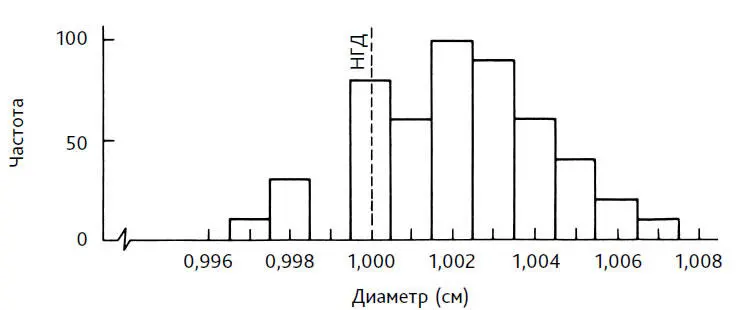
Рис. 24. Распределение результатов измерения диаметров 500 стальных стержней. Очевидно, что контроль н едостоверен. (НГД означает нижнюю границу допуска)
Еще про страх. Гистограмма на рис. 24 просто вопиет об ошибке. Она сообщает нам, что контролер исказил данные. С такой гистограммой можно столкнуться где угодно, практически каждый день. Измерения сконцентрированы как раз внутри допусков и сопровождаются разбросом в данных. Возможные причины для такого искажения очевидны:
1. Контролер пытается защитить тех, кто производит данную деталь.
2. Он не уверен в исправности своего инструмента – опасается, что может ошибочно забраковать деталь; что, если бы инструмент был в порядке, деталь была бы принята.
3. Он не уверен в том, что рабочий правильно пользуется инструментом, что, конечно же, связано с причиной № 2.
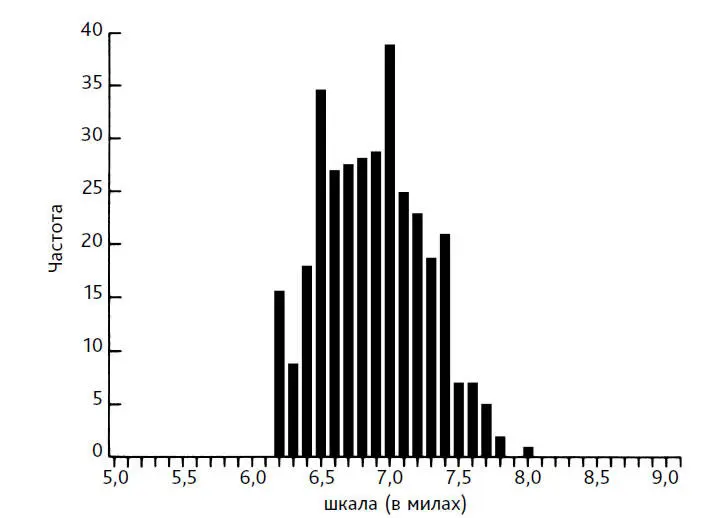
Рис. 25. Распределение измеренных значений. Нижняя граница допуска равна 6,2 тысячных дюйма, верхняя отсутствует
Читать дальшеИнтервал:
Закладка: