Филипп Семёнычев - Стоимость ≠ ценность. Современные методики картирования потоков создания ценности с применением правила 80/20
- Название:Стоимость ≠ ценность. Современные методики картирования потоков создания ценности с применением правила 80/20
- Автор:
- Жанр:
- Издательство:Литагент «Анимедиа»68dd5ea4-ba01-11e5-9ac5-0cc47a1952f2
- Год:2013
- Город:Прага
- ISBN:978-8-0877-6285-1
- Рейтинг:
- Избранное:Добавить в избранное
-
Отзывы:
-
Ваша оценка:
Филипп Семёнычев - Стоимость ≠ ценность. Современные методики картирования потоков создания ценности с применением правила 80/20 краткое содержание
В книге подробно описан метод картирования потока создания ценности в виде простых логических алгоритмов, что позволит использовать её как компетентным в данной сфере читателям, так и тем, кто только начинает пользоваться этим инструментом. Еще одним немаловажным достоинством книги является инновационный подход к применению принципа Парето в сочетании с картированием потока. В книге приводятся инструменты анализа, основанные на вышеупомянутом принципе, сфера применяемости, которых не ограничивается описанным в книге инструментом. Кроме того, вы узнаете о том, какие трудности, в том числе психологического характера, могут встретиться при применении метода картирования, и научитесь их преодолевать. Важно то, что все рекомендации, данные автором, основаны на практическом опыте. Успехов в освоении!
Стоимость ≠ ценность. Современные методики картирования потоков создания ценности с применением правила 80/20 - читать онлайн бесплатно ознакомительный отрывок
Интервал:
Закладка:
Определение задающего ритм процесса осуществляется на завершающей стадии формирования КПСЦ целевого состояния после того, как полностью сформирована вытягивающая логистика потока. Здесь нет каких-либо хитростей и сложностей, самое главное, о чём необходимо помнить – о полной ликвидации «старых» информационных потоков. На самом деле, это достаточно непростая задача, требующая пристального наблюдения до момента стабилизации, т. к. «старые» информационные потоки – это привычки множества людей, которые при изменениях будут стремиться к привычному состоянию. Это может быть ликвидация старых стандартов, схем, маршрутов, переобучение персонала, новая визуализация и т. п. В такой ситуации необходимо сконцентрироваться на возможностях, высвобождающихся у низшего звена управления: время, которое не нужно расходовать на получение, обработку и распределение сменно-суточных заданий, которое можно направить на контроль соблюдения новой системы и решение проблем.
11.1.6. Принцип 5. Выравнивание
Выравнивание или Хэйдзунка (в переводе с японского ящик) – это сглаживание производственного плана по видам и объёмам, необходимое для равномерного удовлетворения спроса. Выравнивание производственного плана по объёмам позволяет равномерно загружать производство, удовлетворяя спрос Заказчика и получая предсказуемый результат (затраты и прибыль). Выравнивание по видам и трудоёмкости позволяет избавиться от перегруза и наоборот, простоя в операциях, изготавливающих тот или иной вид изделия с различной трудоёмкостью. В масштабах времени его можно разделить на выравнивание внутри месяца, внутри суток и смены, что также необходимо учитывать при следовании данному принципу. Так, выравнивание внутри суток не даст требуемого результата при отсутствии выравнивания в течении месяца, и, наоборот, неудовлетворительная организация работ и отсутствие выравнивания внутри суток могут свести к нулю работы по внутримесячному выравниванию.
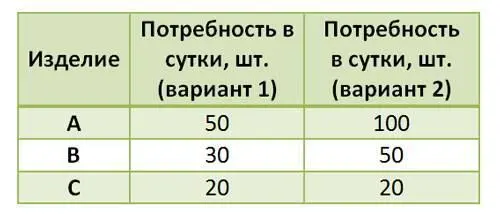
Рис. 11.20
Приведём самый простой пример выравнивания по объёму в масштабе суток.
Доступное время для производства в сутках 480 минут, выпускается три вида изделий, время цикла сознательно не оговариваем, т. к. в данном примере выравнивание происходит по потребности Заказчика (предполагается, что производственные возможности не ограничены).
Рассмотрим первый вариант задачи по выравниванию загрузки в течение смены. Суммарная потребность 100 изделий, время такта 480/100 = 4,8 минуты. Рассчитываем время такта для каждого изделия: А=480/50 = 9,6 минут, В=480/30 = 16 минут, С=480/20 = 24 минуты. Определяем минимальное кратное число расчётным данным, в нашем случае это 9,6×5 = 16×3 = 24×2 = 48.
Другими словами, каждые 48 минут должна изготавливаться равномерная последовательность изделий, которая в нашем случае выглядит как А-В-А-С-А-В-А-С-А-В. Количество повторений каждого вида изделия в последовательности соответствует числу кратности: А-5, В-3, С-2. Эта последовательность для удовлетворения ежедневной потребности повторяется 480/48=10 раз в сутки.
Рассматривая второй вариант задачи, можно увидеть, что логика абсолютно повторяется. Время такта для каждого изделия: А=480/100 = 4,8 минут, В=480/50 = 9,6 минут, С=480/20 = 24 минуты.
Минимальное кратное число так же равно 48 = 4,8×10=9,6×5=24×2, однако последовательность выстраивается немного иная: А-А-В-А-С-А-А-В-А-С-А-А-В-А-А.
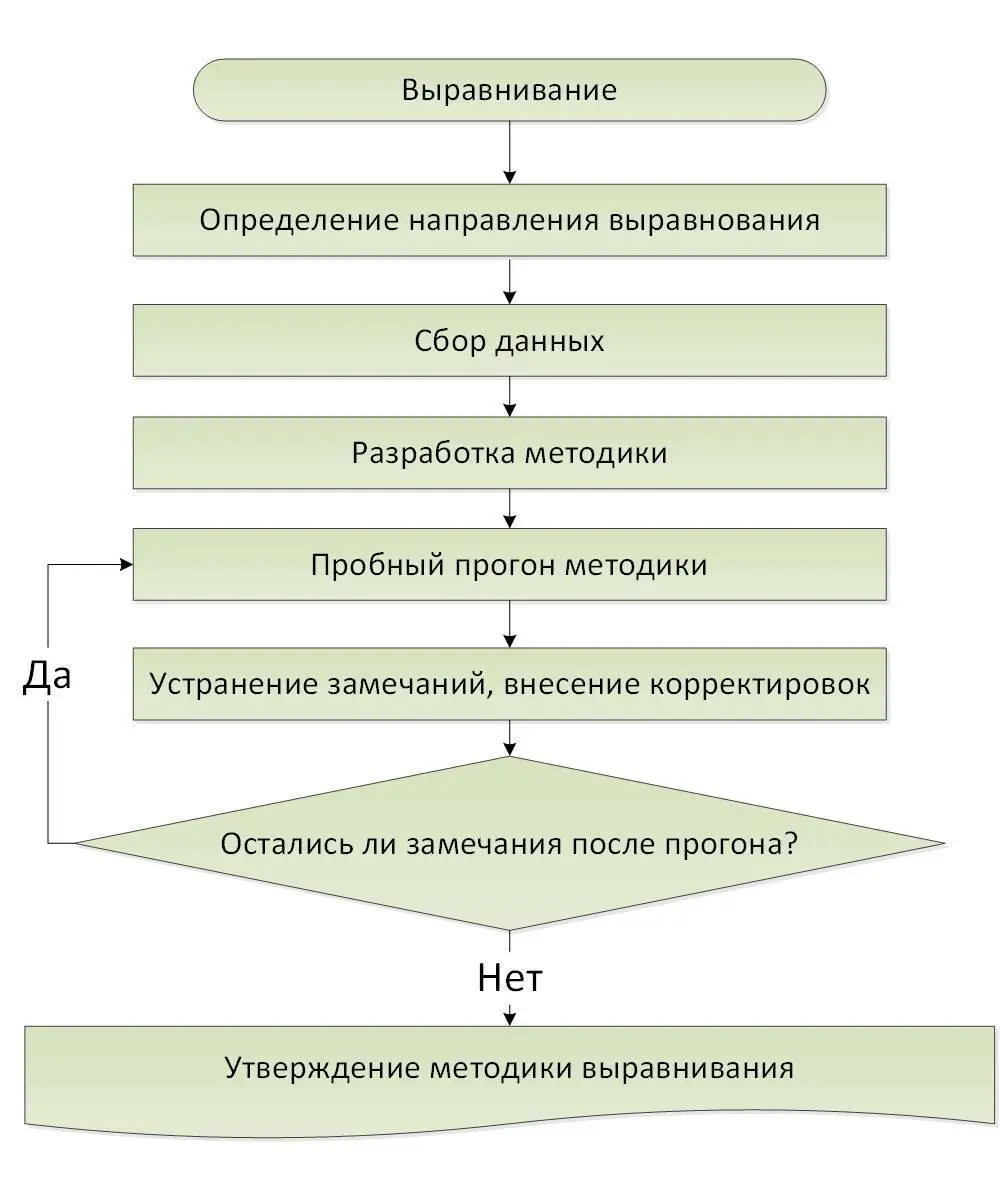
Рис. 11.21
Пример более сложного выравнивания при ограниченных мощностях, т. е. с учётом времени цикла изготовления определённого вида изделия, а также наличием потерь времени на переналадку, описан в разделе «расчёт запасов».
В любом примере выравнивания, какие условия и ограничения не были бы наложены, лежит принцип равномерного распределения производственного задания в соответствии с видом выравнивания, будь то средние арифметические значения плана или более сложные математические формулы.
Алгоритм выравнивания можно представить следующим образом. Вначале необходимо определить так называемое направление выравнивания, т. е. тот параметр, который необходимо выровнять. По сути, этот шаг означает в большинстве случаев определение масштаба выравнивания: год, месяц, сутки и т. п. Как правило, выравнивание в течение длительных промежутков времени, как, например, месяц, осуществляется по количеству изделий, в то время, как в течение суток или недели чаще выравнивается их трудоёмкость.
Следующим шагом собираются необходимые для выравнивания данные: статистика по трудоёмкости, переналадкам и объёму заказов. Несмотря на существование в настоящее время огромного количества различных электронных систем, позволяющих автоматически выравнивать загрузку по объёму и номенклатуре, следующим шагом нашего алгоритма является разработка методики. В данном случае необходимо продумать не просто формулы расчёта средних значений, но определить роли и ответственности участников процесса выравнивания, предмет и периодичность выравнивания, а также функционирование этого механизма на различных уровнях. Так, например, некая электронная система может качественно выровнять загрузку по суткам в течение месяца, однако внутри суток на различных этапах процесса будут использоваться ящики Хэйдзунка. Разумеется, в настоящее время организации с несколькими тысячами видами продукции просто не могут обойтись без качественных электронных систем, однако ориентация на поток создания ценности и логика выравнивания должны сохраняться.
Классическим остаётся пробный прогон методики, т. е. наблюдение за работой методики и устранение возникающих замечаний, проблем и внесение корректировок. Перед утверждением методики и полным переходом на выровненную загрузку необходимо убедиться «в лабораторных условиях» в её работоспособности.
В связи с достаточным количеством общих описаний ящиков выравнивания (Хэйдзунка), в настоящей книге не даётся подробное описание их работы, но делается акцент на общем алгоритме и необходимости проведения испытаний любого выбранного вами метода.
11.1.7. Принцип 6. Определение интервалов управления
Завершающий принцип формирования будущего состояния – определение интервалов управления. Переходить к нему стоит после выстраивания вытягивающей логистики и определения интервалов доставки изделий между операциями. На самом деле интервал управления означает не просто выдачу и подтверждение задания на изготовления какого-либо изделия, а промежуток времени, через который осуществляется периодический контроль процесса производства, т. е. вмешательство и решение возможных возникающих в нём проблем. Таким образом, логично предположить, что интервал управления должен быть как можно более коротким. Но с каким интервалом управлять? Оптимальным считается интервал управления, равный произведению расчетного времени такта на количество изделий в стандартной таре. Данный подход предполагает выдачу задания через определённые отрезки времени, соответствующие времени изготовления стандартной тары изделий при условии выровненного сбалансированного производства.
Читать дальшеИнтервал:
Закладка: