Станислав Астапчик - История и направления развития исследований и технологий индукционного нагрева в Беларуси
- Название:История и направления развития исследований и технологий индукционного нагрева в Беларуси
- Автор:
- Жанр:
- Издательство:Литагент Белорусская наука
- Год:2015
- Город:Минск
- ISBN:978-985-08-1913-0
- Рейтинг:
- Избранное:Добавить в избранное
-
Отзывы:
-
Ваша оценка:
Станислав Астапчик - История и направления развития исследований и технологий индукционного нагрева в Беларуси краткое содержание
Предназначена для ученых и инженеров, работающих в области технологий скоростного нагрева металлов и сплавов, а также для тех, кто интересуется историей развития таких технологий в Республике Беларусь.
История и направления развития исследований и технологий индукционного нагрева в Беларуси - читать онлайн бесплатно ознакомительный отрывок
Интервал:
Закладка:
1966 г. – начало разработки технологии «чулочной» закалки задней полуоси трактора сложной формы;
1967 г. – начало использования индукционного нагрева под горячую резку дисковыми пилами (вместо резцов) вращающихся труб (в несколько раз повышена стойкость инструмента);
1974 г. – внедрение в производство установки для индукционного нагрева стержневой заготовки торсиона подвески сидения; под получение сферического набора металла на конце за готовки;
1975 г. – термообработка дисков турбин дробеметных машин, звездочек конвейеров, тяговых конвейерных цепей и других деталей вспомогательного оборудования;
1979 г. – ВЧ закалка гнезд клапанов головок блока;
1984 г. – нагрев заготовки полуоси с последующей высадкой двух участков с одного нагрева;
1987 г. – создание тиристорного АРН (автоматического регулирования напряжения) МТЗ;
1990 г. – начало применения ЭВМ в делопроизводстве, а затем – в проектировании оснастки;
1993 г. – состоялась встреча ветеранов – энтузиастов индукционного нагрева Минского тракторного завода;
2005–2010 гг. – создание установки для термической обработки балки плуга (филиал МТЗ, г. Сморгонь).
Начиная с четырех простейших деталей в 1949 г., в 1990-е годы обрабатывались уже сотни наименований деталей в 20 цехах, а мощность оборудования достигала 20 тыс. кВт. Как видно из вышеприведенного, сначала это были шейки коленвала, звездочки, втулки, цилиндры, а позже – детали оборонной техники из легированных сталей, полуоси сложной формы, диски турбин дробеметных машин, конвейерные цепи и т. п. детали. В основном использовали машинные генераторы мощностью до 100 кВт и частотой 8 кГц. Поэтому уже в 1959 г. потребовалось создание централизованной преобразовательной подстанции, при этом мощность станка была увеличена до 250 кВт. Затем быстро появились ламповые генераторы частотой 66 кГц.
Приведем примеры разработок Минского тракторного завода, предоставленные нам Л. С. Космовичем и В. С. Барановым.
Весьма удачной разработкой наших первопроходцев является блок автоматического регулирования напряжения [4] (рис. 1).
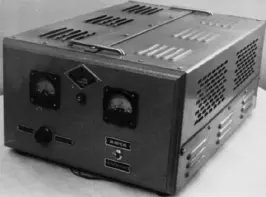
Рис. 1. Блок автоматического регулирования напряжения АРН (МТЗ)
Он был создан в 1987 г. на основе разработки инженера Я. Е. Добиса (1959 г.) и представляет собой тиристорный электронный регулятор, которым были укомплектованы все машинные генераторы (преобразовательные подстанции) ТВЧ МТЗ и автоматические регуляторы напряжения ВНИИ ТВЧ, выпускаемые впоследствии электротехнической промышленностью СССР. Он получил медаль ВДНХ и до настоящего времени применяется на машинных преобразователях МТЗ, заводе шестерен, МАЗе. Позволяет с точностью до 1 % поддерживать напряжение на шиносборке преобразовательной подстанции. Документация передана 24 предприятиям и организациям. Применяется на большинстве машинных преобразователей МТЗ и других предприятий.
А вот следующая история просто уникальна. Сейчас это может вызвать улыбки, когда новейшие транзисторные генераторы имеют частоту до 70 кГц, а тогда… В 1958 г. В. С. Барановым, Л. С. Космовичем, Е. С. Лисковым были начаты эксперименты по закалке бортовых шестерен [5]. Завершены работы были в 1975 г. при содействии М. Н. Бодяко и С. А. Астапчика (рис. 2). Это был предварительный подогрев детали в шахтной печи, а затем в течение 5 с одновременный нагрев мощностью 1000 кВт на частоте 8 кГц всей зубчатой поверхности. Для этого и понадобилось параллельно включить 10 преобразователей по 100 кВт каждый. Правда, включать их можно было только по выходным, иначе останавливалось производство. Все получилось, твердость хорошая, результаты стендовых испытаний хорошие. Но цементация оказалась сильнее и процесс не пошел. Это ли сейчас главное. Главное – смелость и большое творческое желание осилить эту «неподъемную» деталь.
Следующая работа – снова удачная. Работы, начатые в 1966 г. В. С. Барановым, В. Ф. Волчком, Л. С. Космовичем и другими тракторозаводчанами, завершились внедрением [6].
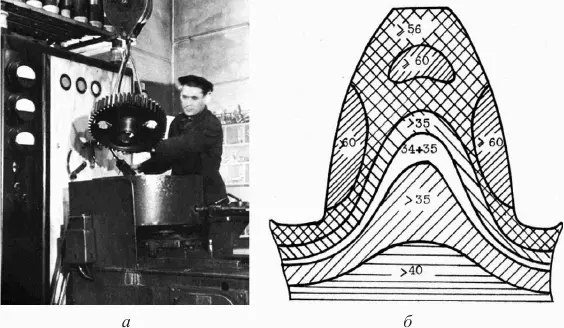
Рис. 2. Поверхностная закалка зубчатой поверхности бортовых шестерен: общий вид установки ( а ) и распределение твердости в сечении зуба в шестерне из стали 50ХГТР после поверхностной закалки ( б )
Это не совсем обычная непрерывно-последовательная «чулочная» закалка (рис. 3), при которой несколько спрейеров охватывают изделия с разными углами охвата (270°, 180° и 90°). Деталь, естественно, вращается. В процессе ее перемещения от спрейера к спрейеру импульсный цикл активного охлаждения уменьшается. В момент выхода изделия из первого спрейера его температура в течение 4 с повышалась до 370 °C. Далее в течение 4 с закаливаемый участок охлаждался во втором спрейере до температуры 180 °C, а по выходу из него в течение 8 с температура достигала 320 °C, далее этот участок попадает в третий спрейер, угол охвата которого составляет 90°. В нем поверхность изделия охлаждается до 120 °C. По мере дальнейшего перемещения закаленная область изделия входит в отпускной виток индуктора, который осуществляет ее подогрев до заданной температуры отпуска.
Несмотря на сложную конфигурацию детали, включающей в себя шпоночный паз, рейку в виде зубчатой поверхности, концентрично оси детали выступающий упорный бурт подшипника и шлицевую поверхность, закалочных дефектов на поверхности детали после многократной закалки обнаружено не было. Надежность процесса проверялась десятикратной закалкой детали, изготовленной из стали 38ХГС, с завышенным содержанием углерода до 0,47 %, после которой трещин обнаружено не было.
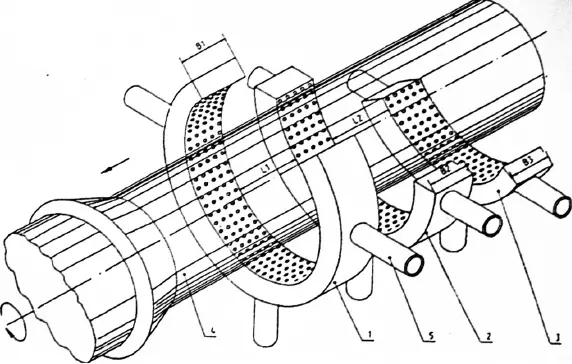
Рис. 3. Схема спрейера для циклической закалки: 1, 2, 3 – спрейеры с углами охвата изделия 270°, 180° и 90° соответственно; 4 – закаливаемое изделие; 5 – штуцер для подачи воды
Стендовые испытания полуоси, изготовленной из стали 40Х и термообработанной по новой технологии, показали 7-кратное увеличение усталостной прочности и ни разу не были доведены до поломки детали ввиду недостаточной прочности испытательного стенда. Лабораторией была спроектирована универсальная нагревательная станция, впоследствии нашедшая широкое применение не только на предприятиях и в институтах республики, но и на других предприятиях бывшего СССР.
И вновь поисковая работа. Казалось, все получилось. Перед закалкой ТВЧ головка блока объемно нагревалась до 200 °C. Требуемая скорость охлаждения после нагрева обеспечила высокую твердость без образования трещин (рис. 4). Получено авторское свидетельство на изобретение. Но при производственных испытаниях на Минском моторном заводе трещинки все же пошли. И работа не была внедрена.
Читать дальшеИнтервал:
Закладка: