Михаил Круглов - Инновационный проект. Управление качеством и эффективностью
- Название:Инновационный проект. Управление качеством и эффективностью
- Автор:
- Жанр:
- Издательство:ЛитагентРАНХиГС (Дело)ed740fe7-6753-11e5-8380-0025905a0812
- Год:2011
- Город:Москва
- ISBN:978-5-7749-0534-8
- Рейтинг:
- Избранное:Добавить в избранное
-
Отзывы:
-
Ваша оценка:
Михаил Круглов - Инновационный проект. Управление качеством и эффективностью краткое содержание
Учебное пособие дает комплексное представление о современных методах управления качеством разработки и производства нового продукта через призму международных стандартов. Читатели познакомятся с наиболее эффективными сценариями, методологией и практикой создания и развития систем менеджмента качества, с требованиями стандартов качественного управления, в том числе семейства ИСО 9000, с практикой лучших мировых компаний в этой области.
Конкретные ситуации иллюстрируют важность, возможность и целесообразность использования подходов, основанных на современном менеджменте качества.
Пособие рассчитано на руководящих работников администраций регионов и отраслей, руководителей предприятий и организаций различных форм собственности, специалистов среднего звена промышленных и научно-технических предприятий, инновационной инфраструктуры регионов.
Инновационный проект. Управление качеством и эффективностью - читать онлайн бесплатно ознакомительный отрывок
Интервал:
Закладка:
• положение о мотивации (цель – создание набора льгот, поощрений и преимуществ);
• положение о КСТ (цель – достижение высоких технико-экономических показателей);
• положение о проведен ии командных собраний (цель – контроль работы команд, установка целей, обратная связь с персоналом);
• положение по инновациям (результат – вовлеченность персонала в процесс непрерывных улучшений).
Таблица 7 .1
Вовлеченность персонала в процесс непрерывных улучшений
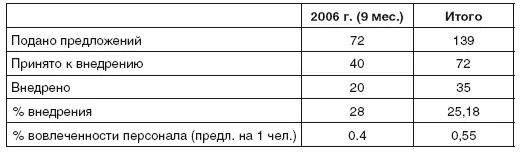
В целом новая организационная система зарекомендовала себя с лучшей стороны, и наработанный опыт был распространен на все электролизное производства в 2005 г.
Следующее изменение коснулось графика работы анодчиков (20 человек). В феврале 2006 г. изменили технологию выливки металла из электролизеров с одного раза в сутки на один раз в двое суток. При этом оптимизировали схему работы кранов. Это позволило организовать работу анодчиков в две смены вместо трех с выполнением прежнего объема работы без нарушения качества выполнения операций. Положительным моментом данного улучшения явилось облегчение условий труда (отсутствие ночных смен).
Работа БЕ по всем ключевым направлениям проекта послужили улучшению в качества обслуживания электролизеров, создана новая организационная культура, изменилась система взаимоотношений между подразделениями.
В производстве была проведена большая работа по анализу потерь и их предотвращению. Примером может быть процесс выливки электролизеров.
• Первый вид потерь – потери перепроизводства: выливка электролизеров и передача ковшей с металлом происходит без учета потребностей литейного цеха. Другими словами, выливка идет по принципу: «я сделал, а надо это следующему участку или нет – меня не интересует». Это приводит к скоплению ковшей на участке шихтовки.
Последствия:
• происходит остывание металла в ковше и требуются дополнительные затраты на его разогрев;
• требуется большее количество ковшей для организации процесса выливки.
Решение. Согласовывать график выливки и литья продукции. Подавать ковш в литейный цех в тот момент, когда будет производиться заливка в миксер. Таким образом можно избежать перепроизводства.
• Второй вид потерь – потери из-за брака и необходимости переделки: при выливке металла из электролизера допущено отклонение от правила выполнения операции и в ковш с металлом попал электролит.
Последствия для литейного производства следующие:
Чтобы вылить металл из ковша сначала нужно пробить корку электролита – дополнительные затраты времени. Пробу на химический анализ с ковша взять невозможно, пока не будет пробита корка – затраты времени, срыв регламента выливки. Электролит оседает на стенках ковша, что приводит к уменьшению полезного объема ковша – уменьшение срока службы футеровки. Для удаления электролита со стенок футеровки ковша его нужно отправлять в чистку – дополнительные затраты времени и труда. Срок службы футеровки из-за чисток уменьшается – трудозатраты возрастают, увеличиваются финансовые затраты на восстановление футеровки. Электролит, попадая в миксер оседает на футеровке миксера – полезная емкость миксера уменьшается, увеличивается количество чисток. Мелкие куски электролита снижают чистоту металла – необходимо ставить ловушки, дополнительные фильтры и т. и. – увеличение денежных затрат и трудозатрат.
Решение. Выполнять операцию выливки в строгом соответствие с установленными стандартами выполнения операций, полностью исключив попадание электролита в ковш.
• Третий вид потерь – потери из-за лишних операций и перемещений. Внедрение пятитонного вакуум-ковша для выливки металла из электролизера (взамен трехтонного вакуум-ковша). Это позволило:
– сократить количество перемещений крана и выливщика на 50 %;
– снизить потери металла.
• Четвертый вид потерь: потери из-за транспортировки. Для корректировки состава электролита необходимо периодически дозировать его фтористыми солями. Предварительно машина с фторсолями разгружается в корпусе (в простенке электролизера), затем электролизник загружает сырье с помощью лопаты в тачку и транспортирует ее к электролизеру, где выгружает ее на электролизер. При таком способе загрузки наблюдались существенные потери дорого сырья (цена за 1 тонну AlF3-26008py6.).
Внедрение машины «HENCON» для загрузки фтористых солей в бункера АПГ (автоматическая подача глинозема) позволило снизить потери при транспортировке. Расход A1F 3снизился на 2–3 кг на тонну алюминия.
• Пятый вид потерь – потери из-за излишних запасов. Ликвидация этого вида потерь потребовала изменения системы материально-технического обеспечения, ее перехода на поставку «Точно в срок». Инструментом является канбан – карта, которая запускает процесс пополнения запасов материалов, когда это необходимо для продолжения производственного процесса. Пример карты, используемой в электролизном производстве для заявки на поставку технологического инструмента, приведен на рис. 7.7.
Также по системе «точно в срок» завозится гасильный шест в корпуса электролиза. До этого гасильный шест завозился по «выталкивающей» системе. Шест завозился 3 раза в неделю в количестве двухтрехсуточной потребности на специальных телегах. В результате существовали потери в связи с излишним запасом, а также наблюдался нерациональный расход шеста и большие трудозатраты на его перемещение в корпусе.
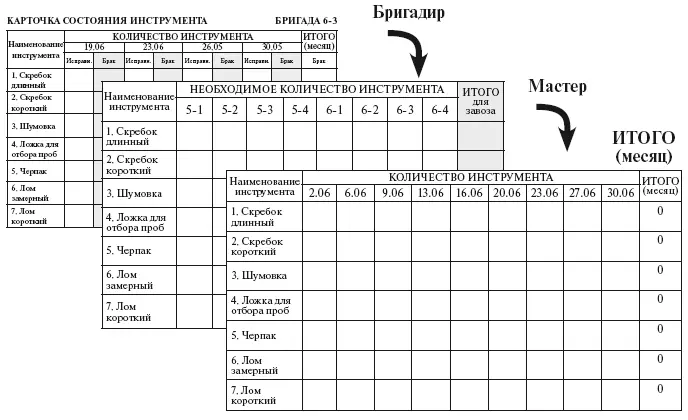
Рис. 7.7. Система заявок и учета технологического инструмента с использованием карточек канбан
В настоящее время некоторые виды сырья, материалы (например, гасильный шест) завозятся по электронной заявке канбан (рис. 7.8) ежесуточно с выгрузкой на каждый электролизер.
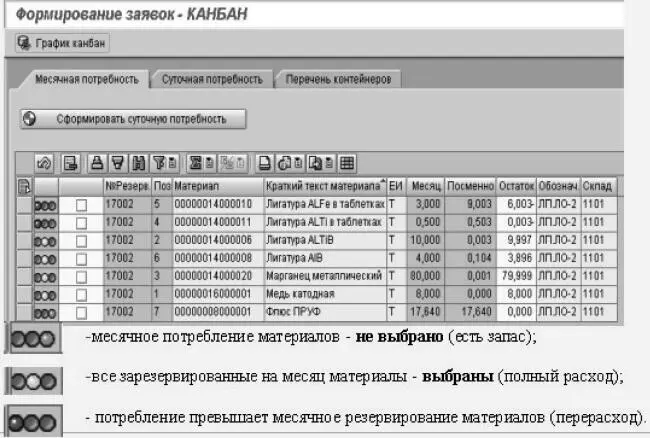
Рис. 7.8. Электронная карточка канбан
Общая концепция поставок сырья и материалов системы «точно в срок» отображена на рис. 7.9.
• Шестой вид потерь – потери из-за простоев и ожиданий. Долгое время при работе с подрядными организациями по обслуживанию и ремонтам различного оборудования возникали трудности следующего характера:
– проблема передачи заявки на исполнение;
– низкая оперативность выполнения заявки;
– отсутствие системы отслеживания, контроля и управления заявками;
Читать дальшеИнтервал:
Закладка: