Дэвид Майер - Практика дао Toyota. Руководство по внедрению принципов менеджмента Toyota
- Название:Практика дао Toyota. Руководство по внедрению принципов менеджмента Toyota
- Автор:
- Жанр:
- Издательство:Array Литагент «Альпина»
- Год:2011
- Город:Москва
- ISBN:978-5-9614-2677-9
- Рейтинг:
- Избранное:Добавить в избранное
-
Отзывы:
-
Ваша оценка:
Дэвид Майер - Практика дао Toyota. Руководство по внедрению принципов менеджмента Toyota краткое содержание
Практика дао Toyota. Руководство по внедрению принципов менеджмента Toyota - читать онлайн бесплатно полную версию (весь текст целиком)
Интервал:
Закладка:
Учитывайте время такта при планировании работы и выборе необходимых усовершенствований. Если вы выбрали слишком большое время такта, вы не удовлетворите спрос, а это хуже, чем выбрать слишком маленькое время такта и превысить спрос (при условии, что для удовлетворения ошибочно определенного спроса вам не понадобилось привлекать дополнительные ресурсы). Всегда проще остановить производство при избыточной производительности, чем увеличить объем производства при недостаточной производительности. Если вы сомневаетесь, лучше ориентироваться на более высокие показатели спроса и меньшее время такта.
Важность визуального контроля
Применение средств визуального контроля – важнейший момент в процессе стандартизации. К сожалению, значение этой составляющей бережливого процесса очень часто недооценивается. Мы нередко слышим: «Они всего-навсего занимаются 5S». Возможно, виной тому примеры средств визуального контроля, которые приводятся чаще всего, скажем разметка пола, которая показывает, где должны стоять контейнеры с мусором и прочие объекты в рабочей зоне. Работники считают подобную разметку лишней – они ведь и так понимают, где что находится! Другой пример – значки, обозначающие место для различных предметов и видов материала. «Мы и так знаем, что и куда класть». Однако когда работника просят рассказать более подробно, например описать процесс поставки материала, назвать его стандартное количество или допустимый минимум и максимум запасов, обычно ответы становятся менее вразумительными.
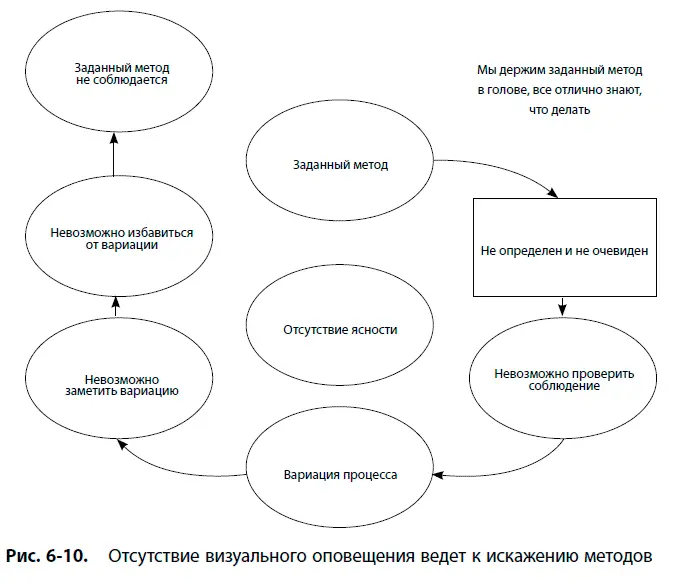
На рис. 6-10 показано, что средства визуального контроля предназначены прежде всего для того, чтобы определить желаемое «нормальное» состояние (стандарт) и быстро заметить отклонение от стандарта. Как мы видели, на каждом рабочем месте требуется соблюдать массу технических условий и процедур. Добиться того, чтобы каждый работник знал их наизусть, практически невозможно, и даже если записать их в тетрадку, это не поможет немедленно вспомнить их при необходимости.
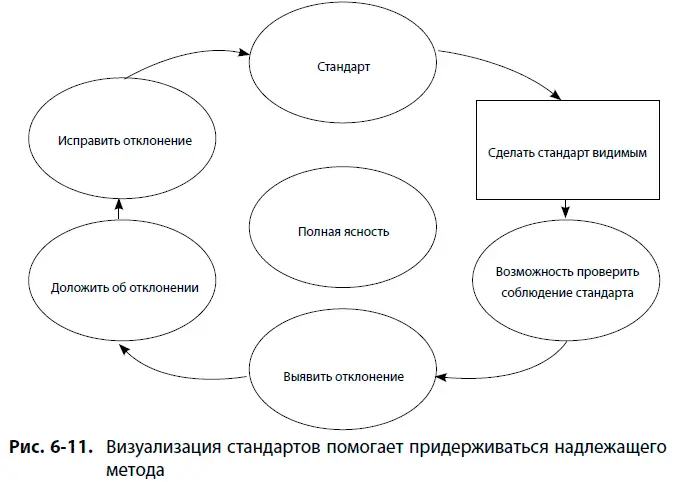
Нередко люди настолько убеждены, что знают стандарты, что любое визуальное напоминание кажется им излишним. Оценить подлинное знание стандартов несложно. Попросите нескольких работников описать конкретный метод выполнения работы. Есть ли возможность установить, что все делается, как положено? Ситуация на окрасочном участке, описанная ниже, говорит о том, что, если возможность быстро оценить соблюдение стандарта отсутствует, отклонения не замечаются и не прекращаются.
Вот что происходит, когда стандарт всем известен, но не визуализирован.

Конкретная ситуация: визуализация подачи изделий на окраску
Речь идет об окрасочном участке с тремя отдельными камерами покраски. На этом участке основная линия разветвлялась на три, каждая из которых подавала изделия к одной из трех камер. При таком разветвлении основной линии для обеспечения потока продукта очень важно, чтобы подача изделий осуществлялась в определенной последовательности с учетом цвета и модели. Это единственный способ избежать чрезмерной нагрузки на какую-либо из камер и заторов на линии. Наблюдение за окрасочным участком (стояние в кругу) показало, что потоку продукта через одну или две камеры часто препятствует затор перед другой камерой. Из-за этого весь процесс подачи изделий останавливался, что сказывалось на показателях совокупного времени простоя линии. Проблема была чрезвычайно острой, поскольку заторы при окраске сдерживали работу всего предприятия (это единственный участок на заводе, через который проходят все изделия) и не позволяли реализовать потенциальные возможности системы в полной мере.
Менеджер участка покраски и работники, которые занимались подачей изделий, единодушно согласились, что при подаче продукции необходимо соблюдать определенную последовательность номенклатуры позиций, и даже выработали единое мнение о том, какой должна быть эта последовательность. Однако при этом каждый замечал, что «они» не всегда соблюдают правила. (Кто такие эти таинственные «они», было не совсем понятно.) Более глубокий анализ показал, что желательный метод (пока еще не стандарт) не имеет четкого определения и описан довольно невразумительно. Это описание включало формулировки такого рода: «Не более двух изделий этого вида в час», «Данное изделие может следовать за одной из трех названных моделей», «Не более шести изделий этого цвета в час». Было понятно, что попытки запомнить предложенную последовательность обречены на неудачу (описание включало слишком много переменных). Эти правила мог выучить разве что тот, кто выполнял данную работу изо дня в день, и если постоянный работник отсутствовал, найти ему замену вне группы было практически невозможно.
Для определения порядка подачи изделий на окраску, который учитывал бы все требования к цвету и ассортименту, была создана команда из трех человек, хорошо знакомых с процессом. Команда потратила почти три дня, чтобы разработать последовательность, удовлетворяющую всем параметрам и условиям. Представьте, как сложно было запомнить такую последовательность наизусть! Неудивительно, что операторы не соблюдали правила, ведь даже сформулировать их оказалось весьма непросто.
Команда разработала доску для визуального отображения последовательности подачи. Завершив операцию, работник должен был передвинуть на доске магнит с цветной маркировкой, показав этим, что задание выполнено. Такие нововведения пришлись по душе операторам, поскольку требования были сформулированы четко и ясно и больше никто не кричал на них из-за того, что они не соблюдают правила. Остановки линии стали случаться значительно реже, а количество изделий (каждое изделие включает несколько субкомпонентов), которые проходили через окрасочный участок в течение дня, возросло с 80 до 110 и более. Освоив систему визуализации стандартов, операторы усовершенствовали доску отображения информации, продолжая уточнять требования и выравнивать номенклатуру изделий (подробнее об этом рассказывается в следующей главе).
Стандартизация как инструмент устранения потерь
Разработка стандартизированной работы – это первый шаг. Он не только позволяет определить стандартный способ выполнения операции, но и предполагает процесс анализа, в ходе которого выявляются потери. Устранение этих потерь – неотъемлемая часть стандартизации. После того как стандарт разработан, а операторы обучены, надо регулярно проверять, соблюдаются ли стандарты, и если нет, то почему. Следует поощрять стремление операторов к подаче предложений по оптимизации процесса. Такие предложения вносятся в стандарты по мере их пересмотра.
Читать дальшеИнтервал:
Закладка: